The embedded computing industry continues to evolve rapidly, driven by the need for high-performance computing solutions in diverse fields such as artificial intelligence, machine learning, robotics, and industrial automation. One of the essential components enabling these advancements is the COM-HPC (Computer-on-Module High-Performance Computing) standard. For developers and system designers, understanding the nuances of carrier board design is critical. This comprehensive article will serve as your definitive COM-HPC carrier design guide, offering in-depth insights and practical strategies to excel in this domain.
What is COM-HPC?
COM-HPC is a state-of-the-art standard defined by PICMG (PCI Industrial Computer Manufacturers Group) to address the demands of next-generation embedded computing. Unlike its predecessor, COM Express, COM-HPC supports significantly higher data transfer rates, enhanced scalability, and improved flexibility for high-performance applications.
The COM-HPC carrier design guide focuses on creating carrier boards that are the foundation for integrating COM-HPC modules into custom applications. These boards connect to external peripherals, provide power, and enable communication, ensuring the COM-HPC module operates seamlessly.
Key Components of COM-HPC Carrier Design
1. Electrical Interfaces
The electrical design of a carrier board is one of the most critical aspects. A robust COM-HPC carrier design guide ensures the proper integration of interfaces such as PCIe Gen 4/5, USB 4.0, Ethernet up to 25Gbps, and multiple SATA channels. High-speed signal integrity and EMI (Electromagnetic Interference) mitigation are vital considerations to ensure reliable data transfer.
2. Power Management
Power delivery is another cornerstone of any COM-HPC carrier design guide. Depending on the application, the carrier board must accommodate power requirements ranging from 12V to 48V. Ensuring stable power delivery with low noise prevents disruptions and maintains optimal performance.
3. Thermal Management
Given the high computational power of COM-HPC modules, thermal management becomes an essential focus area. Advanced cooling solutions such as heat sinks, pipes, and even liquid cooling may be necessary. A comprehensive COM-HPC carrier design guide includes recommendations for designing adequate thermal pathways and placement of thermal sensors.
4. Connector and Form Factor Design
The connectors used in COM-HPC carrier boards must comply with PICMG standards. These include high-density connectors capable of handling data rates up to 32 GT/s. The carrier board’s form factor should align with the module’s size, ensuring seamless mechanical integration.
5. Peripheral Integration
An effective COM-HPC carrier design guide also provides strategies for integrating peripherals such as displays, sensors, and storage devices. This involves selecting appropriate interfaces, optimizing layouts, and testing compatibility with various peripheral components.
Steps to Develop a COM-HPC Carrier Board
Step 1: Requirements Analysis
The first step in the COM-HPC carrier design guide is to assess the application’s requirements. Identify the computational load, peripheral interfaces, and environmental conditions the carrier board must accommodate.
Step 2: Schematic Design
Translate the requirements into a schematic. This involves selecting components such as voltage regulators, connectors, and ICs. During this phase, ensure compliance with COM-HPC standards.
Step 3: PCB Layout
Designing the PCB layout is critical in the COM-HPC carrier design guide. Pay close attention to high-speed signal routing, power delivery networks, and thermal management zones. Utilize simulation tools to verify signal integrity and thermal performance.
Step 4: Prototyping and Testing
After completing the layout, produce a prototype of the carrier board. Conduct extensive testing to verify compliance with COM-HPC specifications, electrical performance, and mechanical compatibility.
Step 5: Iteration and Optimization
Refine the design based on test results. This iterative process ensures that the final product meets all performance criteria and is ready for production.
Challenges in COM-HPC Carrier Design
Despite its benefits, designing a COM-HPC carrier board is not without challenges. High-speed signal integrity is a significant hurdle due to the increasing data rates. Similarly, thermal management for high-power modules can be complex and may require innovative solutions. A well-structured COM-HPC carrier design guide addresses these challenges by offering practical advice and design tips.
Applications of COM-HPC Carrier Boards
The versatility of COM-HPC carrier boards enables their use in a wide range of applications:
- Industrial Automation: Ensuring real-time control and monitoring in factory environments.
- Medical Devices: Powering advanced imaging systems and diagnostic tools.
- Robotics: Supporting AI algorithms for autonomous navigation and manipulation.
- Edge Computing: Enhancing data processing at the edge of networks.
- Telecommunications: Driving next-generation communication technologies such as 5G.
Each application has unique requirements, emphasizing the importance of a tailored COM-HPC carrier design guide to achieve optimal results.
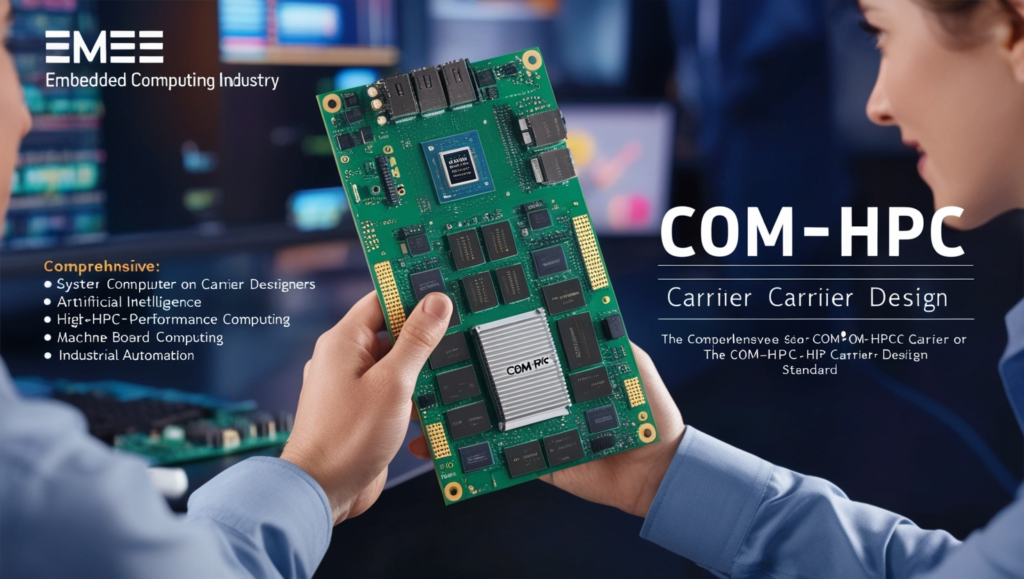
Future Trends in COM-HPC Carrier Design
As technology advances, the future of COM-HPC carrier boards will be shaped by trends such as:
- Higher Data Rates: Supporting PCIe Gen 6 and beyond.
- Enhanced Miniaturization: Developing compact carrier boards for space-constrained applications.
- Advanced Cooling Solutions: Implementing innovative thermal management techniques.
- Increased Automation: Leveraging AI for automated design and testing processes.
By staying abreast of these trends, a COM-HPC carrier design guide can remain relevant and valuable for future projects.
FAQs on COM-HPC Carrier Design Guide
Q1: What is the role of a carrier board in COM-HPC systems?
A carrier board connects the COM-HPC module to external peripherals, providing power, communication, and interface support.
Q2: How does COM-HPC differ from COM Express?
COM-HPC offers higher data transfer rates, better scalability, and support for more advanced applications compared to COM Express.
Q3: What are the key challenges in designing a COM-HPC carrier board?
Challenges include maintaining high-speed signal integrity, ensuring robust power delivery, and managing thermal performance.
Q4: Can a single carrier board support multiple COM-HPC modules?
A well-designed carrier board can support multiple modules, provided it meets the power and interface requirements.
Q5: How do I start with a COM-HPC carrier design project?
Analyze the application’s requirements, followed by schematic design, PCB layout, prototyping, testing, and iteration.
Q6: What tools are commonly used in COM-HPC carrier design?
Tools such as Altium Designer, Cadence Allegro, and Ansys are popular for schematic design, PCB layout, and simulation.
Q7: What industries benefit most from COM-HPC carrier boards?
Industries such as industrial automation, telecommunications, robotics, and medical technology benefit significantly from these boards.
Q8: How do thermal management strategies vary in COM-HPC carrier design?
Thermal strategies depend on the module’s power consumption and include heat sinks, heat pipes, and liquid cooling systems.
Q9: Are there standard sizes for COM-HPC carrier boards?
Yes, COM-HPC modules follow specific form factors, and carrier boards must align with these dimensions for compatibility.
Q10: What future developments can we expect in COM-HPC carrier design?
Expect advancements such as support for higher data rates, miniaturized designs, and integration of AI-driven design tools.
Conclusion
By leveraging this COM-HPC carrier design guide, designers can confidently navigate the complexities of creating high-performance carrier boards, ensuring success in a rapidly evolving technological landscape.